-
Mast Step - Cutout?
I searched the forum but couldn't find an answer. I'm making a new mast step as mine is shot and want to know what is the extra cutout for?
-
mast step
Your mast bottom has a cast Almag fitting with a fore-n-aft
key that fits into the 'half mortice', I believe.
The open portion was to allow mast electrics access below.
The bottom of the wooden maststep has a subtle curve
carved into it that exactly matches the crown of the cabin.
The Manual suggests having an aluminum one cast as a
replacement.
You can use the old one as a pattern, using something
like bondo to do smoothe filling and fairings to make a
nice pattern for the foundry to use.
Take a look at Commander #155 'Mephisto Cat' -Galley
However, you will see there is no discussion here about
the making of the step. And the cross opening remains
just as much a mystery.
Last edited by ebb; 05-19-2016 at 01:32 PM.
-
Image is of the bottom
The image is of the bottom of themes step. So the "half mortice" (red arrows) is actually what I'm questioning. Also, has anyone ever added a water drain path to the step? Seems like it's needed but who knows.....
-
red arrows
The depth of the mortise(s) would match the two square protrusions
of the mastbase casting -- which is 1l/16" -- mortice might be 3/4".
{LATER EDIT: This is wrong. See post #6 below here. The fore
and aft thru hole is where the tenons of the mast base fit.}
There is in my original base casting, which is essentially an aluminum
bowl with two cube-like tenons, an open 1 1/4" diameter hole dead
center through the bottom.
This used to have a piece of pipe extended into the mast, obviously
to lead mast wiring through a matching hole in the mast step and
a matching hole through the cabin top. Condensation & rain water
leaking thru these holes have caused a lot of grief over the decades.
Many have closed off the thru-holes when the mast was removed, and
have lead their wires through a watertight deck fitting near the mast
step, wires lead out the side of the mast 6 to 10" above the bottom.
Assume your original 'wire' holes are closed off one way or another.
Assume like almost everyone else you will not be able to remove
the casting from the bottom of the mast without violence. Corrosion
has welded it to the mast extrusion. Imco it should be removed and
something else put in its place, but it's a lot of work. Only my opinion,
but a G-10 insert could be made machined to engage the original
maststep mortise. You would need considerable thickness, but G-10
can be glued with epoxy and tapped for machine screws.
The top of a new G-10 insert would be flat. The insert will be bedded
in with something like Dolfinite, so that it can be taken out again in
the future. The mast inside will be sealed, altho you will see light
through various holes, and the main sheave open 'box' at the top.
You want a drain hole through the mast wall at the level of the insert.
The original casting includes a 5/16" ledge for the mast extrusion to
sit on. The casting used screws to fasten it on to the extrusion. On
A338 it all corroded (and actually expanded the mast) into a single
mass. Sacrificed about an 1 1/2" of mast height by cutting it all off.
Made it up with a taller maststep.
IDEA (to completely seal the inside of the mast from leaking below.)
If you have the mast off the boat, have access to the casting, and
have closed off the original wire access holes into the accomodation
through the maststep. And are able to, maybe , bondo shut the
center hole between the two cubular tenons in the casting... I'd
be considering, if I was not willing to remove the casting, a way to
fill up the bowl completely. You discover that the base casting is not
a solid block but a thick walled bowl about 1/2" at its top to 3/4"
where the ledge under the extrusion is seen at its very bottom.
When the mast is back up and vertical again, drill a couple 3/8"
holes through the mast wall (port and starboard), just above where
you're sure the top of the casting terminates -- about 1 1/2"above
the end of the mast extrusion, where you will find the 1/8 mast wall.
Or predrill those holes while the mast is down and the step is not
in the way. The thought is, to use these holes to inject liquid rubber
into the casting bowl and fill it up to the level of the holes.
This is just an idea. Have not actually done this.*
You certainly can drill holes lower down, but the thickness of the
casting will make it difficult to inject liquid rubber. You will use a lot
more rubber to fill the whole cavity. 8 to 10oz I guess, but more likely
to fill to a known level because your fill holes on either side of the
mast will end up as topping drains for the rubber plug.
Theoretically the liquid will not fill above the two holes if you have
placed them level with each other. I would choose liquid rubber
rather than epoxy because it is least likely to leak out. Epoxy would
be easier to inject. But also more likely to glue the mast to the step,
get out of containment within the mast.
And if you ever have to cut it out, you'll wish you used rubber.
In the interest of later mast removal, make sure you do not glue the
mast to the boat. Amazing what damage a crane can do if the mast
does not readily lift off the step.
Littlegull has a forward lowering mast with a removable G-10 insert
with a slope inside. Where there's a hole to let any water out.
~~~~~~~~~~~~~~~~~~~~~~~~~~~~~~~~~~~~~~~~~
* Plasti-Dip $7, 14.5oz, may be the cheapest liguid rubber around.
It's for dipping tool handles for a softer grip. It weathers fairly well
exposed. Internally it should last a long time. Used it enough to
know that if you try to save a partial can, it'll be hard by the time
you get back to it. When the mast is vertical: use 2oz TAP Plastics
Syringe Applicators from TAP $3.10. You can dip the nozzle into
the rubber, pull back on the plunger to load the tube, wipe off the
excess, jam it all the way into a fill hole in the bottom of the mast
....and push the plunger! You want to be quick reloading. If you use
white you might see what's going on by shining a light through the
2nd hole. Just an idea...
Last edited by ebb; 05-27-2016 at 08:15 AM.
-
Photo of top of mast step
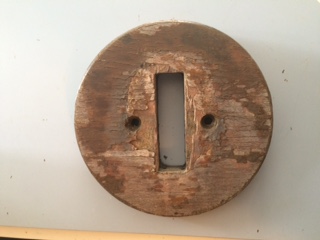
This is what I have for a mast step (top view). I don't see accommodation for the square protrusions. It's just a mortice for the whole casting. At it's thickest it's 1.5". I didn't measure the mortice depth.
If you can't see the image please let me know. I'm a newbie with images here.
Last edited by roythomas; 05-20-2016 at 10:09 AM.
-
original maststep
Roy.
Just took a look at my original maststep and it IS exactly like yours.
That fore-and-aft slot is where the square tenons go.
The 1/8" mortised cross is on the bottom side of the step.
Been a long time since I decommissioned A-338. Looking at the
maststep here makes me think differently about that cross mortice,
which as you show, and what I have here, is NOT to receive the
mast base casting in any way. I was entirely very wrong.
First of all, The mortise is athwart the boat, port and starboard.
And the indentation is only about 1/8" deep. (On my step the router
bit has left a telltale of slight circles in the wood. Meaning, it was
intentially placed there for a reason.)
And it's definitely on the underside of the step.
OK. Obviously it housed a piece of metal. A plate was anchored in
place by the two #20 bronze screws that went through the step
and cabintop and into the oak strongback. It probably had a
larger hole in the center into which a wire conduit tube was fitted.
And since we know there originally was a piece of pipe conduit there,
extending up into the mast to fair lead internal mast wire below -- I'd
guess the 8 to 10" (guessing) conduit probably screwed into the plate
to keep it erect. Remember various photos showing this piece,
always cockeyed or bent. Which could happen if the plate was
threaded... hardly any thread in 1/8' plate thickness.
The 'sump' created there by the mast base casting collects any water
trapped in the mast, funnels it thru the step, leaking around the plate
into the composite and into the strongback below.*
Given some of Pearson's 'wham-bam-thankyoumam' solutions I've
run into... that plate should have been bronze to survive the airless
environment under the step next to those bronze lag screws. But it
probably was 304 and probably corroded and disintegrated in far
less time than five decades it's been hidden under there.
Imco, nobody would restore this original design, running wire below
thru the mast. Causes too much trouble..
So that would solve the mystery, imco.
~~~~~~~~~~~~~~~~~~~~~~~~~~~~~~~~~~~~~~~~~
*Fresh water leaking thru the mahogany/phenolic plywood maststep,
not only will eventually compromise the step but also rot the balsa
composite core in the deck below it. The hole for the wire was left
unprotected in the original installation. Some of us fixed it by partially
routing out the cabin top under the step and replacing the 'tunafish'
with solid fiberglass.
Some have also replaced the wood step with aluminum or G-10.
By the by, the rotting of the balsa and the pressure and weight of
the rig, also flattens the curve in the cabintop -- as well as influences
the plywood that makes up part of the strongback and bulkhead.
Which see.
~~~~~~~~~~~~~~~~~~~~~~~~~~~~~~~~~~~~~~~~~
Opinion. You know how a stick in water looks bent?
..............That's why I never take a bath.
Last edited by ebb; 05-30-2016 at 08:10 AM.
-
Yay!!
I was thinking there is no structural reason to replicate the original step and had similar concerns about proper water drainage you just mentioned. I may route a little groove on the bottom to allow water to escape without pooling in the step. Thank you for investigating. Now I can't decide if the step is a consumable because of eventual deterioration and therefore ok to varnish and replace every 5 years or should I try to fabricate something permanent and epoxy/fair it in. I'll go with consumable for now. It's and easy "make" as far as I can see. My boats previous owner already rerouted the electrical to a separate fitting on deck next to the mast. Sadly he never epoxied the drill holes and I now have rot in that location (among others because of his half baked installs).
-
consumable maststep
That plywood step is a very special plywood. It is surprising that they had it in the 60s.
It's made with very thin veneers, with either mahogany or another tropical wood, and
glued with a phenolic urea under high pressure.
My maststep, once on a very weathered Ariel, is still in good shape after 50yrs exposure.
The plywood has not deteriorated at all. Eyeballing the step from different angles, it
is a little bent... it is slightly concave on top. But ready to go, imco, another 50 years.
My mast was shortened because of corrosion, and now has a taller maststep made with
a modern version of phenolic mahogany plywood called BS1088 Meranti Hydrotec.
For its price, it is the finest marine plywood on the planet. Bar none. If I had to make
a new maststep, that's what I would choose.
The old step is carved from 1" material. In thickness it is very slightly 'wedge' shaped:
the front of the step is 13/16" thick, the aft side 1". It is also curved on the bottom to
match the crown of the cabin it sits on. You can see these anomalies expressed in the
veneer laminations.(Spring a batten across your cabintop to see if the curve is still fair.)
If you want to groove the very bottom of the maststep, and have repaired, replaced
if necessary the balsa core of the cabin composite, and closed off any water entry thru
the cabin top.... I would groove it athwartship, and clear across the whole diameter
of the bottom, so that as the boat tilts the groove always drains port and starboard.
Bamboo skewer might be used to keep the scupper clean.
If you are reusing the maststep, it has NO soft spots, might sand it well with 80 grit.
Then soak it in agood quality laminating epoxy slightly thinned with xylene. Brush on
a final coat of epoxy and sand it smooth. (Don't think this step absolutely necessary!)
Wipe it down with isopropyl alcohol. Then UV varnish or paint it.
This is all imco! Good luck!
Last edited by ebb; 05-31-2016 at 12:22 AM.
Tags for this Thread
Posting Permissions
- You may not post new threads
- You may not post replies
- You may not post attachments
- You may not edit your posts
Forum Rules