-
spastic plastic
In the Ariel that has me, the predominant factory fabric is mat and woven roving (an irish lament
)
When you grind the paint and gunge off the original polyester, revealed is a greenish tone to the plastic. And the the sweet smell of styreen. Epoxy has an amber look sometimes and isn't sweet smelling.
You can recognize the roving by its huge basket weave, and the mat by its translucent and messy look, usually where a prospective boat buyer won't be looking.
The forepeak has some nice work in it - both the factory's and the PO's backing plate.
The backing plates in A338 were easy to recognize squares and rounds of Ariel laminations - all about 1/4" thick.
The Ariel had backing for cleats and hardware. Looks they they forgot plates in your Triton - the bolts do look long enough!
If those rusty bolts are 50years old, they are in great shape! If they are replacements, they
are an inferior grade of stainless like 304. But the rust may be caused by the nut and/or washer being a different grade of steel.
Some of those old repairs look OK, but others look like hurry-ups. Handiwork looks like several different PO's or yard worker's. Some look like epoxy, some polyester. If they are polyester you can probably slip a sharp chisel under an edge and almost pop it off.
If epoxy you might do the same, or at least separate the new from the original with more persuasion.
Can guess there was little prep done previous to pasting the tabs on. Chiseling them off, you'll find, is a lot more fun than grinding. Watch it tho, a sharp chisel can also find a cloth seam in an old Pearson lamination....and before you know it you're peeling the hull!
If you seriously are going to grind on the boat, you have to have tools that aren't going to kill you.
The dust you create will do that. Recommed you cough up some serious cash and get a Festool vacuum, top of the line.
With that get one of their side grinders and also a heavy duty 5" sander.
You have to buy their system, including their sanding disks.
I used a Festool sander for later work in the boat to sand off paint and lamination ridges. The old polyester is tough stuff.
The system draws dust in thru the tool, into the vac, which has a HEPA filter.
You can cook a turkey dinner right next to someone grinding fiberglass. You can work in your boat without a mask ! !
Your tool is wired to the vac - pull the trigger and the vac goes on - release it and the noise shuts down. I see them in the boatyard these days. Fein vacs and tools are a distant cousin to Festool, I wouldn't bother, and they cost too much as well.
The large Festool vac has a huge capacity. You can have the vac in the boat with you, it won't throw glass particles out its exhaust.
Since I'm a curmudgeon, I find the level of German engineering very impressive, but irritating. The worst work on the boat you'll ever do is the prep on the hull.
If you have kids, you'll be leaving the Festools to them in your will. I borrow from the shop at the vineyard here. I've never heard of a problem with any one of them. Treat yourself, your lungs will love you for it!
Would try to forensic the reasons for the obvious repairs in the lazaret.
If you find your hull/deck join is in trouble, and you embark on sealing the seam with tabbing,,,,you will have places you can't get to inside.
I would get an osilating tool with a plunge blade and ream the seam in those places from outside. And refill the seams with epoxy or rubber bonding adhesive.
Last edited by ebb; 11-17-2013 at 06:20 PM.
-
Quite possibly the worst job one could undertake on these smallish hulls. Dirty, hot, poor visibility, nearly impossible angles, all compounded by the need to achieve adequate surface preparation so your glass job isn't just a recreation of the previous, marginal job. But do it. You will have all that much more confidence when it comes to one of our boats major flaws. Confidence, or maybe prudence is what we are gaining here, because as you pointed out many of these boats have travelled miles without incidence. Furthermore, any other job you will need/want to do on her afterwards will pale by comparison. Ebb's technique in post #53 would be a great way to address the seam and get the beginning of a sexy rub-rail.
Ebb brings up a point not often enough addressed. Pay for the quality tools up front. This job, done properly, will take three or four times longer than you anticipate (unless you are a veteran at this stuff). I opted for the grind and clean method that involved suiting up in tyvek coveralls, bandana, full face respirator, hearing protection, crawling into the worst spot, grinding until I was either out of breath from exertion or it just got so dusty I couldn't see. then try to climb back out after squirming around into a position completely incompatible with the orientation necessary back out of the route taken in, blow off with a compressor making absolutely sure NOT to wipe any sweat or scratch any itch. Take a quick minute to muster the will and then go back into the mess with the extended shop-vac hose to pickup as much dust as possible. Then if you need a closer look at the area give it a good washing with a simple green solution to see if you're going back in with the grinder or acetone. I may have left out a step or two but you get the picture. It is hard to justify the cost before hand, but, if you are going to do more glass work or modifications it will pay off in the end.
As you are probably well aware of, this site has a wealth of knowledge in its threads. even though some of these threads have been quiet for a year or two, this group was so far ahead of its time the information is just as relevant today as it was then.
My home has a keel.
-
Thanks Ebb, Tony for your timely encouraging words. I just come back from a couple of hours of grinding the worst tabbing job in the Triton history. I was wrong about the tabbings being done by amature PO's. They were done by amature Aero Marine employees! I looked at another friend's west coast Triton (belonging to Rob Heggen). It turns out that the tabbings in his lazarette look similar to mine (i.e. same material and not painted) except his tabbings are done 100 x better than mine and looks the way they should be. Seems like I drew the short straw on the hull deck tabbing.
I figure if I am going to go through this dreary job I might as well start as soon as possible. No sense postponing the inevitable pain. Here are some of the photos I took while I was goint through the port side cockpit lazarette. Starboard side tabbings are in similar albeit somewhat better shape. I noted three types of tabbing problems in Blossom. Firstly, the outer layer is waved cloth. At times they are barely attached to the hull or deck. There is no dbout they have no holding power whatsoever. Secondly, the inner layers are woven rovings that Ebb mentioned above. There are a few spots where I can tell that there are air pockets behind the rovings. I am not just talking about the air pockets in the recess of the toerail. You can see in some of the pictures there are circular shaped voids in the tabbings. Those are results of air pocket after the tabbings covering it has been ground out. Lastly, you can see that the overlap between the tabbings and hull and deck are marginal in my opinion. In some places the overlap is only an inch or two. As for the thickness of the total tabbings I was not able to determine for sure. It appears that there are a couple layers of rovings at least in the lazarette area which is a lot better than I thought. I would like to add two layers of 6 and 8 inch biaxial tape with adequate overlap.
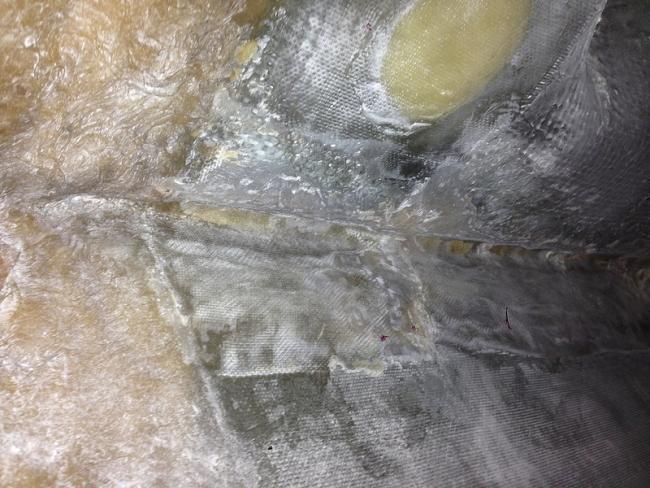
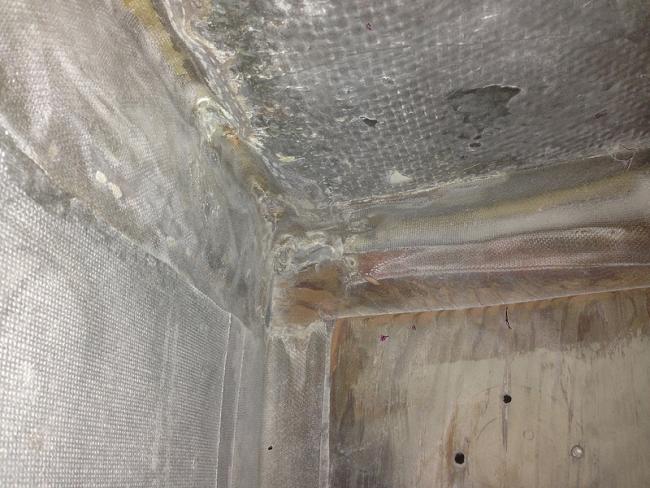
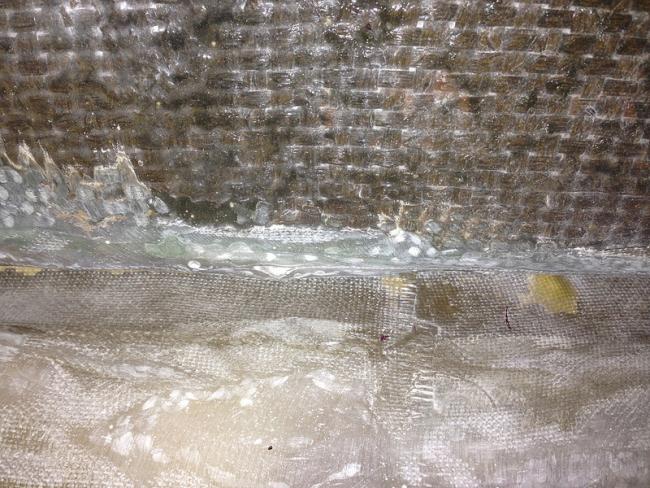
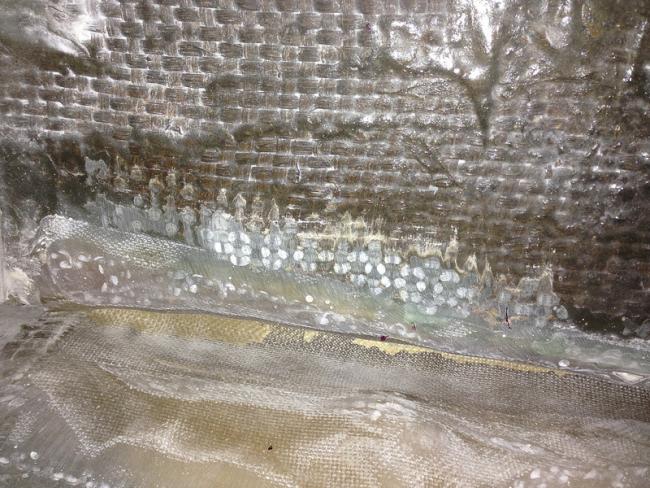
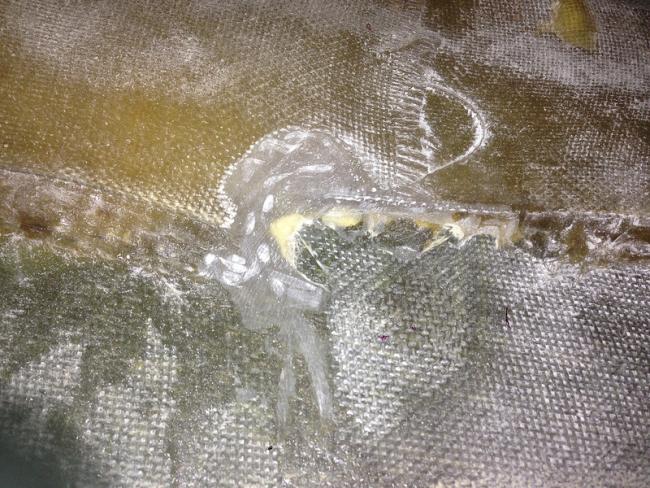
I appreciate the tip on proper tools. I never heard of Festools before Ebb mentioned it. I have not decided if I will get them or not as they are expensive. One question I have is what tool you used and how you grind out the recess under the toerail. There is no way to get into it with an angle grinder. I have not address it. I was thinking of using Dremel tool with some type of sand paper or grinding stone but they don't seem to be the optimal solution. I would like to use something a little more powerful. Any ideas will be much appreciated.
Last edited by Triton106; 11-17-2013 at 07:42 PM.
-
Those voids look all too familiar. The ones that didn't open with the 4 1/2" angle grinder got punctured with a dremel tool with a burr bit. The toerail cavity was attacked with a 4 or 5 inch diameter wire wheel that I mounted on a 6 inch length of all-thread and chucked the mighty power drill. That pretty much chewed out any unsaturated glass in the cavity. Before I taped the seam each of the voids were dabbed with straight epoxy and while still in a green state filled with thickened epoxy. Then the whole seam got another pass with the grinder with much less aggressive grit before washing. That helped the tape lay flat (as possible) to avoid replacing the original voids with more voids of my making. Hope that makes sense and helps you out a bit.
My home has a keel.
-
You know you might get good info from Commodore Triton his self. Rob knows more about Tritons than anyone, and works on them for a living.
Photos show a fine job of prep and the what-looks-like impromptu tabbings look pretty solid and attached pretty good.
Still think that if any of these bandages look suspicious to you, test their adhesion by trying to slip a sharp Stanley chisel under an edge and gently pry on it....see if it wants to lift off. If you can follow the 'seam' with the chisel, I would assume a bad bond and remove it.
When you see those obvious empty white glass flaps (you show a patch of small ones) I'd use the same chisel or a utility knife with a Lenox blade (Irwin has decent bimetal blades) and just core them out. See what they covering up. Fill them with epoxy gell with chopped strand.
The deck in our boats were laminated upside down in a mold. Most of that lamination is OK.
After it was turned right side up and glued to the hull, any additions (by anybody) had gravity and access going against it.
Tabbings overhead might very well sag and make a 'bubble'. I found unsaturated white roving in A338.
Tap any suspicious area, if it sounds hollow cut it out, especially if there is a possible leak. Might have water in it.
You can fill a deep overhead cavity in stages with structural filler, so that the goop doesn't fall out. Fill it a couple times until flat and maybe add a piece of cloth to blend it in.
If you have to do it all at once, this I've done for vertical repair with structural gel.
Have a piece of plywood roughly the size of the repair, with a piece of mylar stapled on in. (Mylar is a 'stiff' film. Backed by ply, it'll makes an absolutely flat surface when braced over a repair.)
Prop this against your freshly gooped depression, press firmly to squeeze the filled cavity flat thereby forcing epoxy into cracks & holes (and extra filler out from under the edges of the ply persuader. If done conservatively, it'll cut your grinding time.)
The trick is to brace it in place with one or more 'spring battens'. Bendy pieces of fir lumber that are just a little longer than any opposite bulkhead, or stringer, or the hull itself...that you are able to bend the batten slightly between the plywood and a hard place....to create firm compression. You want to hold and put some positive pressure on the ply pad... without breaking the battens. More battens , more pressure. Pressure is stronger coming from sticks that are just about to straighten out, but can't.
When set, disassemble - mylar peels away - and you have a glass smooth mirror surface of the filler you used.
You can do this with many repairs, and not just flat (use thinner ply or polyethylene sheet against the hull, for instance). Big diameter coves can be made with pieces of pvc tube, covered with seranwrap or mylar Thin ply can be bent and twisted - using spring battens.
The technique (if it can be called that) compacts the bandage/repair, squeezing fillers and fabric, making a bond as good as your prep.... and you get an almost too perfect surface as reward.
I've added epoxy and glass cloth and biaxial any where I thought the hull could use it.
A338 has a consistently thin hull.... that Pearson did NOT make progressively thicker as they laminated from sheer to keel.
The Ariel hull is mostly 5/16" thick in the turn of the bilge and keel where the 2500lb lump of lead is encapsulated. Quality control problem.
We know polyester is not water-vapor proof. Certainly gelcoat is not water proof. A338 has at least one coat of some sort of 2-part epoxy everywhere on the hull from the water line down around the keel. Much of the interior is epoxy coated up to the sheer.
Awlgripped topsides were prepped and filled with epoxy. The bottom extensively epoxied from waterline down.
Coating olde raw polyester with epoxy will seal and help support the historic polyester. Imco it's the best present you give your classic plastic.
Naturally there will be someone who says polyester needs to 'breathe'.
Prefer the boat to purrrrrrs.
A nice shiney white 'tank coating' will make those diffricult areas of the boat (forepeak/lazaret) easy to keep clean, easy to sponge, easy to illuminate, easy to find sttuff. AND easy to forget those cheap-shots & blemishes that once stared you down.... when its all shiney white.
However, that is another kettle of....epoxy.
Last edited by ebb; 11-23-2013 at 12:30 AM.
-
toe rail cove
To go along with Tony's post.....here's my two feet of electric cord.....
I've had success with SANDING SLEEVES, the ones that slide over a 1/4" shank rubber drum
that you expand by tightening a nut (the wrong way) on top. Not all sanding sleeves are created equal.
You want best quality mahogany-colored aluminum oxide sleeves in coarse grit, like 80 or 60 grit.
So far, I trust Klingspor* abrasives. www.woodworkingshop.com + 800-228-0000
Find the correct diameter drums and sleeves. So that you can clean out both sides and 'bottom' of the cove inside the toe rail with the same effort.
Looks like you can use a range of widths. Ariel toerail cove was quite even, clean and open, probably due to stingy laminations -and a rediculous attempt at bonding the seam with a stingy layer of fiberglas mat..... that worked!
Shorter drums are probably more manuverable, and cheaper to replace.
If you jam them the covers can tear apart....so loose fit is best.
Get more than you think you need, because it's rough going for even a well made sleeve.
Imco your best bet tool for this project is an ANGLED DRILL.
I've nearly wore out my old special order 3'8" chuck Milwaukee angle.** And 100s of sleeves, nearly all coarse grit.
Klingspor catalog has a generic for $59.95 (TZ20000) that maybe's worth trying.
This 55 degree angled design is perfect for boats.
You grasp the body of tool in one hand, it becomes a bionic extension with the working end at an ergonomic slant.
-And the angled gear part of the tool is relatively tidy, allowing you to get IN close and personal anywhere,
including the tight cove up in the corner against the hull.
Don't believe a right angle drill has anywhere near the versatility of a half angled drill.
.................................................. .................................................. .................................................. ............................................
Have never figured out how to freehand a stone bit. They clog or dull or disintergrate immediately.
Equally useless are the conical rasps of different profiles. Too short and dangerous, they come already dulled.
There are carbide coated disks & burrs. Wouldn't use them where I couldn't keep an eye on them. $$$ and wear quickly.
.................................................. .................................................. .................................................. .............................................
The Klingspor has other helpers:
3" wide rolls of 80 grit aluminum oxide with cloth backing (like SANDING BELT.)
Make yer own sanding blocks with plywood pieces. Stick the two together with 2-sided fiberglass carpet tape.
Make reach-in paddles with thin ply and sanding belt on both faces. (Keep yer fingers out of the cove!)
You lightly score the cloth side with a utility knife and snap the piece off the roll.
.................................................. .................................................. .................................................. ............................................
Another great tool used on both wood and glass is a Nicholson CABINET RASP #49.
This is a versatile 7/8" wide half-round rasp-file with staggered teeth on both sides, about 12" long OA with about 9" of teeth.
I use it without a handle for every little task. It's a shame to use it on fiberglass..... but sometimes you have to.
This is a treasured woodworking tool. Expensive. A joy to use, doesn't make much noise, and it's always ready to get you out of trouble.
Don't know who has them right now. Have to find them 'on sale' to afford one.
Get three.
.................................................. .................................................. .................................................. ...........................................
A Fein type oscilating MULTITOOL would be a safer power tool to use. There are mutiple brands. Not one of the idiot imitators has come out with a more versatile angled design. Right angle tools are OK in a right angle habitat, like house or shop. but have limited use on a boat. (Exception is the dogleg plunge cutter)
Some have a carbide rasp attachment. But I found (the Fein rasp) too coarse to be useful. An imitator may have a mo'betta rasp for the cove. I've really used few attachments that came with 'multimaster kit'.
Haven't tried this: For some of your what-looks-like very narrow coves - maybe carpet taping a loop of sanding belt over a 'dog leg' plunge blade might get into those narrow places. Possible !
[Elsewhere here I've put down the Fein as being WAY W A Y too expensive for what you get, not only the power head but its sanding and cutting attachments have insulting prices. I'd try Harbor Freight. And then look for better bimetal cutters on the internet. You can see what Fein has in the Klingspor catalog. Then look elsewhere. Most after-market blades (Imperial) fit all mutitools. Ocilating multitools are held by the body which quickly get too HOT to handle. Source: forums.]
If you have a Bosch multi and want a plunge cutter, try their new Carbide Blade OSC114C - actually cuts metal ! 
.................................................. .................................................. .................................................. ...........................................
*Klingspore are the progeny of Klingons
** McMasterCarr has a Milwaukee 3/8"chuck 3.5Amp 55degree angle drill (0370-20) = $132.50
[Brutilized my 15yearold, never replaced anything, altho the cord at the tool is leaving - dislike gear chucks that have to have keys attacht to the cord.
Last edited by ebb; 04-23-2014 at 09:54 AM.
-
I stopped by Blossom this evening to test the fit of the Tide's Marine Strong Track I received yesterday. I will post the installation of the strong track and Code Zero furler in a separate thread once I am done with them. Anyway, it was blowing 20-25 knots gustting to 30-45 in the marina when I got there. The marina is situated in the Oakland Estruary on Alameda Island. It certainly was not an auspicious night for working on the hull deck joint. But ever since I read Ebb's suggestion I have been wanting to test the soundness of the bonding of the hull deck tabbings with a sharp chisel. One reason I feel this is important is that when I looked at Vento Dea's hull deck damage I can see that the fiberglass tabbings appear to have been ripped clean off the hull, indicating a very poor state of bonding.
As you can clearly see from the pitctures below the tabbings between the anchor locker bulkhead and deck on Blossom are also not well bonded. I could almost tear off the outer layer the entire length of the bulkhead by hand. The tabbings between the bulkhead and hulll are in better shape. However, I still would not know if they will survive a knock down by a freak wave. So my plan is to cut out the entire bulkhead and make a new one. I will then reinstall the new bulkhead in a ring of foam cushion between the bulkhead and the hull and deck. In addition, I also intend to install two longitudinal stringers that run the entire length of the v-berth and the anchor locker. As I mentioned before, when I painted the hull a few years ago I noticed stress cracks in the gelcoat all the way around the hull where the bulkhead is. I suspect the lack of the stringers to support the forward hull and the tabbing of the bulkhead directly to the hull are the main reasons for the stress cracks.
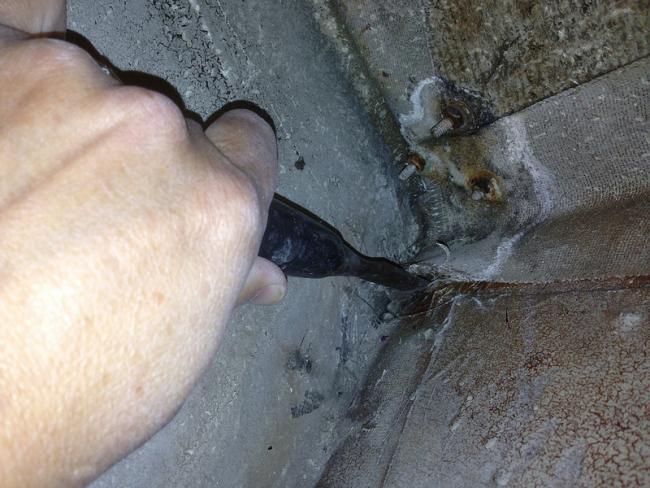
Last edited by Triton106; 11-21-2013 at 10:18 PM.
-
detab
That's amazing.... and instructive!
If those tabbings are factory, ie original, then it's textbook that polyester is not a glue.
And therefore you cannot expect a bond when using polyester resin to tab a cold seam.
If the tabbing was 'after market', and the resin used was epoxy.... then prep, or DFO, or resin, can be to blame.
May have had a discussion on a thread here once about bulkheading (Tony G?).....
The main aguement for 'floating' a bulkhead is that you (hope to) avoid point loading.
In other words, if you install a plywood bulkhead tight to the hull,
you're going to create the problem (like Pearson did), such as you describe with gel coat grazing on Blossom's hull.
The bulkhead is 'photographed' on the exterior hull.
Textbook technique is to space the bulkhead off the hull by, say, 1/2" and attach it floating to the hull with tabbings. To avoid the hollow, you'd use 1/2" foam rubber strips to get form fit....and tab away. But running fillets on foam gasket could be problematic.
This may be good for major bulkheads. It definitely spreads the point load. And would work.....but I'm not total on that.
I'm an egg crating fan, (mostly persuaded by what I considered is the starved hull on Ariel338) and therefor worked in a number of minor 90degree web intersections with the hull - lockers, mostly in the galley and accommodation.
It seems unneccessary to offset all these minor bulkheads.....with foam. Because one could argue that there are multiple sharing point loads spread out over an area of the hull.
The hull would have to be very thin indeed to photograph web construction thru the hull. Depends on your definition of egg-crating!
Imco the crazing on your hull comes from the hull being unsupported on either side of the bulkhead.
LittleGull's hull had horizontal hollows on either side of the STRINGER - a mahogany 2X2 tabbed to the hull about 15" down from the sheer - the stringer stopped abruptly at the main bulkheads: mast and cockpit. I added 'extensions' to this stringer running into the V-berth forward to the bow - and aft from c'way blkhd to the lazaret blkhd behind the cockpit.
litlgull also had vertical hollows on the hull forward of the mast blkhd, where there were no stringers. - extending below the waterline.
Wanted to even the stresses of the stringer's obvious pointload out to the ends of the hull. Wasn't going to remove them.
A338 topsides hollows became evident when I spent two months endlessly filling, fairing and long-boarding prior to painting. [Ebb'sGallery pg7#126 & pg10#126.] However the 'bumpouts' on A338 didn't show any gelcoat crazing per se'. But long-boarding removed gelcoat on all the highpoints.....bulkheads and stringers.
The hull's permanent topography happened when it was being laminated. But it's fixable cosmetically if you go to the trouble of arduously filling and fairing. They are, perhaps, more unsightly than dangerous. Original blkds now have added tabbing, and all furniture is tabbed or filleted in web or box like constructions.
Could argue that a line of gelcoat crazing showing up on the hull is a sign of stress....of glass laminate in the hull stressed continuously, and might act as a zipper and open the boat up....on a dark and stormy night. VientoDeo's hull zippered open, not at the seam, but above the seam where glass was forced into a radical angle to make a flange.....obviously broken strands of glass there. They broke during layup 50 years ago.
Cove fillets are called for where glass lay-up changes direction.
And stopping the tabbing on the hull is done gradually...tabbing is always stepped to the hull.....espeially at major bulkheads.
It's plausable that a Triton or Ariel rigged and loaded for cruising, punching through waves where it experiences dynamic forces on its quarters, on its mast and rigging - or yanked by mooring loads - grounding on shore....... can TWIST and zipper open hidden and unintentional construction seams.
Didn't remove major bulkheads in the Ariel , some sloppy tabbing came off easy, tite stuff I left on.
But both cabin bulkheads in A338 were substantially altered.... the main under the mast (and the lower shroud 'knees')... and at the companionway where nearly half was removed to create a quarter berth (but with an added wide 'rib' constructed where the blkhd had terminated.
The cheat was to add wide fillets and mutiple tabbing on either side of the original bulkhead. Thinking is that would spread the pointload of the original that was glued in hard (without a space.)
This is where bialial tape, or strips, was used. Did it backwards from norm by filliting first,
then laying in a narrow strip, then wider strip, then finishing with the widest....thereby ending with fairly smooth super tabs. If you can't do it all at once, dry edges can be reduced/faired - easily if still green - with BACHO 625ergo carbide scrapers. "Don't go down to yer boat without them!"
They come with belt holsters too!
SUGGESTION for a new major bulkhead:
I think, altho didn't have the opportunity in A338, that pointload from a new hard plywood bulkhead can be reduced or eliminated
by first laying down graduated biaxial strips on the hull where the bulkhead is going. Eg: 2"/4"/6"/8".
In other words strengthen and support the hull and spread the load befor a nicely fitted ply blkd goes in. Finishing off with similer graduated tabbings from bulkhead to hull. Imco strapping the hull like this might enable the hull to resist twisting. Of course, this is all opinion.
Using biaxial will allow neat work on compound shapes because you can tease the material ... into neat straight lines of buildup.
Neat enough anyway, so that grinding is kept minimum. "This ain't no grand piano..." as a carprenter once said to me.
Aye know...aye know...but it is..... Blossom!
Last edited by ebb; 12-14-2013 at 09:42 AM.
-
Been away for a while.
I did make some progress in the meantime. I finished retabbing the hull deck joint in the lazarette. After grinding out the joint I filled the low spots (especially the cavities in the toerail) with thickened epoxy. I then retabbed the joint over with two layers of 5" and 8" biaxial tape. I did not take any pictures as I was rushing to get it done but I did spot a couple of white spots which indicate to me air bubbles under the tape. I am a little disappointed by that but overall the joint is much stronger than it was before. I hope I will never have to find if it is strong "enough".
In the anchor locker I likewise ground out and then retabbed two spots under the deck that had been poorly tabbed at factory that I mentioned in my ealier post (see pictures in that post). That was straight forward. On the other hand, the bulkhead deck joint was a little more interesting. I was able to pull large pieces of outer tape (weaved cloths) off by hand and was able to easily chisel out the remainer. The inner tabbing was made from fiberglass matt most of which were not properly wetted out (much like the pictures in Vento Dae). I was able to chisel that out fairly easily. For the most part the tabbing came off cleaningly, only a small piece of plywood came off with the inner tabbing. It was so clean that I had a second thought about replacing the bulkhead.
Thanks Ebb for the detailed treatise on proper bulkhead installation. A lot of timely and good ideas to think about...
Last edited by Bill; 12-13-2013 at 10:33 PM.
Reason: Off Topic
-
Dang
Don't know if the old adage 'looking a gift horse in the mouth' works here. It's not about how rotten the boat is. Maybe it's about which end of the horse we're looking at.
Knees in the Ariel were pieces of exterior plywood (thick lams with voids in the middle - but nicely tabbed) at right angle to the hull which brings the plates up thru the deck also at a right angle to the toerail.
Found that to be backarseward and ended up with macho plates slapped on outside the hull, parallel with the toerail and loads on the bolts.
Read once that the weight of the boat should be able to be supported, HUNG, by the rigging.
Took that as gospel and way overbuilt what littlgull has now. Probably too much.
Just heard this one...
There were these three guys going to the quillotine during the French Revolution:
a priest, a drunkard and an engineer. "Any last wish," asks the guillotinair to the first.
"I'd like to go face up to God in heaven, where I'm going," says the priest. The great
knife falls.... but stops short of slicing his head off. "It's a miracle!" yells the crowd,
"Set him free! Set him free!" So he is let go. The drunkard is next, and he says,
"I wanna go to heaven too, face up for me." Same thing happens, the knife stops
just befor it chops off his head. It's a miracle! It's a miracle! set him free! So he's let go.
Now, it's the engineer's turn. "I want to go face up, too..!" Just as the executionor is
about to pull the lever, the engineer yells, "Wait, wait, I think I see what the problem is."
Last edited by ebb; 12-14-2013 at 11:54 AM.
-
LOL... Ebb, that's a good one. Being an engineer myself I admit us engineers love to solve problems regardless if the problem needs to be solved or not, who will benefit, how the solution will be funded, etc, etc... I also admit in many ways I approach boat projects the same way - solve problem first, define goal later, if ever. Sad isn't it? But you live and you learn. I am getting better at defining goals first and then finding solutions.
I think someone must be eating my postings. For two days in a row now I have posted new postings and verify that they are posted only to find later in the day they are deleted for some reason. Maybe they were not posted correctly. This will be my test posting to see if it will disappear again.
-
T106, the subject here is hull to deck, not the restoring of a particular yacht. Please search to find an appropriate thread for other subjects.
-
Ok, that explains the disappearing posting mystery. I commend the Forum for its discipline. At the same time it would be nice to get an explanation or at least a note to the effect. I literally posted the same postings three or four times thinking that I must have done something wrong in the posting process.
-
Peter Theis (Solsken, A-82) wrote the following Email in response to a notification that there were new posts to the deck joint thread. I believe he wanted this conversation posted to that thread – Peter is asking for comments.
-Moderator
>>>>>>>>>>>>>>>>>>>>>>>>>>>>>
Here's a comment from one of my sailing friends. The crew dropped his Renegade off the hoist as I recall. That is the fall he is talking about. He got a new boat out of that disaster.
Peter
-------- Original Message --------
Subject: Re: Reply to thread 'Deck joint-Who, What and When'
Date: 03 Dec 2013
From: Rex Miller
To: Peter Theis
Not having seen the joint on your boat it is hard to assess the applicability of the thickness. On my Renegade the hull turned in and the deck was epoxied to the top of the turn. Not super thick. It was thru bolted through a hollow toe rail but the bolts did not go through the deck lip as I recall. No amount of tightening would stop leaks at the through bolts. The jib sheet car track was on top of the toe rail, compounding the problem. The hollow had been filled with a goop that dried over time. Tightening the bolts just collapsed the toe rail. I fixed the problem by making stepped aluminum blocks with a 1/4 inch step 1/2 and inch wide to address the thickens of the deck section.
The major damage to the Renegade when it fell was at the deck to hull joint splitting for over 8 feet. Within one inch of the outboard edge the deck became cored and was substantially thicker until it reached the coach house turn. The stability of the monocoque hull relies on the hull to deck joint so relying on a small surface area, of less than a inch wide, of contact area, which to boot would have be a secondary bond. It was in my opinion a poor and inherently weak design at that critical junction. The failure described below does not surprise me in adverse conditions.
Had the joint been shoe box joint it would have supplied much greater strength.
The Ariel, Renegade and the Triton were similar designs and had much in common and much to commend them, but not the construction of the hull to deck joint. The 5200 would add some strength to the joint as it is primarily an adhesive.
On Mon, Dec 2, 2013 at 1:23 PM, Peter Theis wrote:
I'd be interested in your thoughts on this disaster. When I rehabbed my Ariel, the baby brother to the Triton, I used a Dremel tool to establish a groove outside of where the deck and Hull were joined. I had had leakage through that joining but never a clear break. I filled the groove with 5200 to join the deck and hull and close any leaks when the boat was healing. It seemed to have worked, at least so far. The deck overlay creating the gunwale where they join is very thin and there is not much for the epoxy or the 5200 to adhere eight at the juncture.
-
Wow, another case of a torn hull deck joint albeit from an accident. I don't know the details of the fall but can imagine that the force of the impact from the side of the hull deck hitting the water must be similar to the force created from a slamming by a freak wave. The bottom line is this Renegade hull deck joint was not strong enough to survive the fall. The natural question is then could any Triton/Arial/Commander/Renegade survive such a fall. I don't know the answer. The bottom line for me is that they need to if you intend to take the boat offshore, which is the reason why I am going to process of adding additional tabbings internally to the hull deck joint. If you are just daysailing or racing around the boyd then all you should care is if the hull deck joint is leaking or not, unless your boatyard drops your boat from the travel lift in that case you might be lucky and get a new boat.
Posting Permissions
- You may not post new threads
- You may not post replies
- You may not post attachments
- You may not edit your posts
Forum Rules